Basics Knowledge of Grease
DEFINITION
The grease is a semi-fluid to solid product, which is dispersed by a thickener in a base oil (liquid lubricant). Other additives or fillers are commonly included to impart special properties.
COMPONENT
Lubricating grease is composed of three substances: thickener, base oil (liquid lubricants), and additives.
2.1 Thickener
In lubricating grease, a substance composed finely divided particles dispersed in a liquid lubricant to form the product’s structure and adsorbed base oil into skeleton to form a plastic semi-solid grease called thickener. Thickener mainly used are fatty acid metal soaps, organic compounds and inorganic compounds.
2.2 Base Oil
Grease is a structural skeleton of the two-phase dispersion system, base oil is the dispersed phase. Base oil, which accounts for 70% to 98% of total grease, is main body. Itself is a liquid lubricant and plays an important role for grease.
The type and character of base oil determines or affects some properties of grease, such as lubrication, evaporation, low temperature property and compatibility with sealing materials. Base oil includes mineral oil (petroleum based lubricants), synthetic oil (such as synthetic hydrocarbon, ester oil, silicone oil etc.)and so on.
2.3 Additives
Grease additives were added to the grease in order to improve its performance, which can improve the inherent properties of grease, and impact new extraneous performance. Lubricating grease additives include: the structure improved materials, antioxidants, metal deactivation agents (metal deactivator), rust inhibitors, corrosion inhibitors, extreme pressure agents, oily agents, antiwear agents additives, as well as all kinds of fillers.
PHYSICS AND CHEMISTRY INDEX AND SIGNIFICANCE
3.1 Penetration
Penetration: The depth that the standard cone of penetrometer falls into the lubricating grease sample when released to fall under its own weight for 5s. The penetration is measured in tenths of a millimeter. Worked Penetration: The penetration at 25°C, without delay, of a sample after 60strokes in a standard grease worker.
Prolonged Worked Penetration: The penetration of a sample after it has been worked more than 60 double strokes(usually ten thousand or one hundred thousand strokes) in a standard grease worker at a temperature of 15 to 30°C.
Penetration of grease is a measure of consistency (viz, soft and hard level) indicators. The National Lubricating Grease Institute(NLGI) classified greases into nine grades according to their consistency as measured by the worked penetration. The classification system is as follows:
Screen Shot 2013-11-28 at 12.26.44 PM.png
3.2 Dropping Point
A sample of lubricating grease contained in a cup suspended in a test tube is heated under conditions of test, the temperature at which the first drop of grease falls from the hole into the bottom of the test cup was recorded as dropping point of the grease.
3.3 Colloidal Stability (Oil Separation)
It named an ability that grease in the long-term storage and use to resist oil separation. Colloidal stability in fact is the combination of stability of base oil and thickener.
3.4 Evaporation Loss
The evaporation loss of grease is a tendency to adversely affect the original performance characteristics caused by evaporation of base oil in the storage and use. The evaporation loss of grease is usually in terms of loss in weight of the sample (mass percentage evaporation loss).
3.5 Mechanical Impurities
The mechanical impurities are others solid material (such as sand, dust, rust, metal shavings, the solid raw material impurities, etc.)besides thicker solid additives. Containing mechanical impurities is very dangerous, which may cause friction surface of the abrasive wear, increase bearing noise, metal shavings, metal salts and accelerate grease oxidation.
Detection method of impurities commonly used is microscope, examines different diameters of impurities under the microscope, then cumulative count, and finally determines impurity by standard.
3.6 Mechanical Stability
Mechanical stability of grease (as known as shear stability) is the performance that when the grease’s structure was damaged by mechanical force, changes of consistency is occured. The mechanical stability of grease was in terms of the change value of penetration.
3.7 Oxidation Stability (Chemical Stability)
The ability in the storage and use to resist oxidation process called oxidation stability. Oxidation stability is one of the important properties of service life, especially more important for long-term use at high temperature. If oxidation stability is poor and long-term exposure to air, the acid will increase, and surface of grease will harden. It not only cause the corrosion of metals, but also cause mechanical damage due to bad lubrication.
The sample into a test missile filling oxygen required, and carry out oxidation test under a certain temperature and time, how much lower pressure of oxygen or oxidation of the acid value of grease remark the capability of anti-oxidation of grease.
3.8 Corrosion
A prepared metal strip is totally immersed in a sample of grease and heated in an oven at a specified temperature for a definite period of time. Commonly used condition is 100°C for 24h. At the end of heating period, the strip is removed, washed, and compared with the Corrosion Standard.
This test method covers the detection of the corrosiveness to metal of lubricating grease.The main corrosive reasons are: Firstly, grease itself contains corrosive substances such as water, excessive free acid, alkali and reactive sulfide materials etc.; Secondly, due to their own poor oxidation stability, grease will generate new organic acids oxides in the process of storage and use.
3.9 Bearing Life
A single row ball bearing with the test lubricating grease is rotated at a high speed under a constant load and selected temperature. Total running time is determined at completion of the test as a measure of the durability of the grease.
3.10 Similar Viscosity or Apparent Viscosity
Similar viscosity or apparent viscosity of lubricating grease is the variable to shear rate at certain temperature. The standard uses Pa.s as units.
3.11 Low-Temperature Torque
A open ball bearing is packed completely full of the test grease. The bearing remains stationary while ambient temperature is lowered to the test temperature and held there for 2 hours. At the end, the restraining force of the bearing was measured, and the starting and running torques were calculated. Through this test method the determination of the extent to low temperature performance of grease was covered.
3.12 Flow Pressure
Fill the sample into the test machine, at the specified temperature rise pressure in a certain time interval, measure the momently pressure of the test nozzle when grease was squeezed out. The indicators are used to examine grease mobility at room or low temperature.
3.13 Timken Test
On Timken Extreme Pressure Tester, fill the grease-feeding device with grease, run for 30s to break-in at the uniform rate. After the load has been applied, scores the wear scar on the metal block to determine load carrying capacity of lubricating greases.
3.14 Four-Ball Test
The Four-Ball EP Tester is operated with one steel ball under load rotating against three steel balls held stationary in the form of a cradle. The rotating speed is 1770rpm. Lubricating greases are brought to 27°C and then subjected to a series of tests of 10s duration at increasing loads until welding occurs. The representations are as follows:
PB value: A maximum load in the experimental conditions the ball didn’t wear.
PD value: A minimum load in the experimental conditions the top ball with three stationary balls weld. ZMZ: An index of grease resistance in the extreme pressure under full load performance.
LWI: An extreme pressure capacity index under the load the lubricant decrease to minimize wear. Anti-Wear Characteristics: On the Four-Ball Wear Tester, three steel balls are clamped together and covered with the lubricating grease, a top steel ball is pressed with a force into the cavity formed by the three clamped balls for three-point contact. The temperature of the lubricating grease specimen is regulated at 75°C and then the top ball is rotated at 1200rpm for 60min. Lubricating greases are compared by using the average size of the scar diameters worn on the three lower clamped balls.
3.15 Water Washout Characteristics
The grease is packed in a ball bearing, the bearing is then inserted in a housing with water impinged on. The amount of grease washed out in certain time is a measure of the resistance to water washout of the grease.
3.16 Shear Stability with Water
Fill grease in roller with a certain amount of water, then shear under required number in consecutive, measure change value of penetration after the test.
3.17 Roll Stability with Water
Fill the sample and a amount of water into a weighted roller inside a rotating cylinder, measure the change in consistency of a sample, as measured by cone penetration, after a specified amount of working in a test apparatus.
3.18 Corrosion Preventive Properties
New, cleaned, and lubricated bearings are run under a light thrust load for 60s to distribute the lubricant in a pattern that might be found in service. The bearings are exposed to water, then stored for 48h at 52°C and 100% relative humidity. After cleaning, the bearing cups are examined for evidence of corrosion.
3.19 Corrosion-Preventive Properties Under Dynamic Wet Conditions
New, cleaned, and lubricated bearings are tested partially immersed in water (distilled, synthetic sea water or sodium chloride solution) under no applied load at a speed of 83 rpm in a predetermined sequence of running and stopping for a period of approximately one week. After cleaning, the bearing rings are examined and rated according to the degree of corrosion.
3.20 Conical Sieve Oil Separation
The weighed sample is placed in a cone-shaped, wirecloth sieve, suspended in a beaker, then heated under static conditions for the specified time and temperature. the sample is tested at standard conditions of 100°C for 30h. The separated oil is weighed and reported as a percentage of the mass of the starting test sample.
3.21 Pressure Oil Seperation
Use the pressurized oil separator to impel oil out from grease, and then examines oil amount by pressure.
3.22 Oil Separation by Centrifuging
Pairs of centrifuge tubes are charged with grease samples and are placed in the centrifuge. The grease samples are subjected to a centrifugal force at 50°C for specific periods of time, measure the amount of oil separated. This index used to determine the extent of oil separation by centrifuging.
3.23 Friction and Wear Properties
This laboratory test method using the High-Frequency, Linear-Oscillation SRV test machine to quickly determine extreme pressure properties of lubricating greases at selected temperatures specified for use in applications where high-speed vibrational or start-stop motions are present with high Hertzian point contact.
3.24 Elastomer Compatibility
Compatibility of lubricating greases with standard elastomer is evaluated by determining the changes in volume and hardness that occur when elastomer coupons are totally immersed in a grease sample for 70h at either 100 or 150°C or as required by the lubricant specification.
USE OF LUBRICATING GREASE
4.1 Advantages and Disadvantages of Lubricating Grease
4.1.1 Advantages of Lubricating Grease
(1) Grease lubrication, does not require complex sealing device and oil supply system, can greatly simplify the bearing external dimensions, is conducive to miniaturization and lightweight device.
(2) Grease has good adhesion and sealing, has good ability maintain on the friction surface, so grease can use in open and poor seal friction working conditions.
(3) Grease has long life, less number of supplying oil, not often to add, so it is more favorable to use grease in the friction parts which are often difficult to refuel.
(4)Lubricating grease has more thickness film and wider range than lubricating oil. It can start below its freezing point 10ô?°—of base oil.
4.1.2 Disadvantages of Lubricating Grease
(1) Grease is a semi-solid can’t flow at room temperature, so it is difficult to add or change grease on friction parts, and not very convenient to clean bearings.
(2) It’s difficult to separate the mixing water, dust and wear debris. If relating to oil, impurities usually submerged in the lower part, or is easy to remove by oil filter.
(3) Grease has difficulty to mixing, so owns large heat and poor cool. (4) Not applicable for high speed conditions.
4.2 Influence Factors for Choosing Grease
4.2.1 Purpose of Using Grease
Choosing grease, the purpose should be clear at first. Grease can be divided into friction, protection and sealing three categories, while choosing grease depends on which is the dominant role.
4.2.2 Temperature of Lubricant Parts
On the lubricant parts of mechanical friction, high and low temperature and temperature change plays a decisive influence on the use and life of lubricating grease, operating temperature of lubricant parts is an important basis for choosing lubricating grease.
4.2.3 Load of Lubricant Parts
4.2.4 Speed of Lubricant Parts
Grease is a flow system, its similar viscosity can change with shear rate. Therefore, the physical and lubrication of lubricating grease are particularly sensitive to operation speed of lubricant parts, which is different with lubricating oil.
4.2.5 Environment and Media of Lubricant Parts In Contact
The environment and media of lubricant parts in contact have a dramatic effect on and the performance of the grease, therefore, choosing grease should be carefully considered.
4.2.6 Method of Filling Grease
The method of filling grease has manual and pump filling. Painting, injection, grease guns filling, grease cup filling and so on belong to manual filling.
4.2.7 Comprehensive Benefit
There are a variety of grease to meet the mechanical requirements, but choosing grease, you can’t only care about the price, but also wonder the grease whether extended lubrication cycles, reduced maintenance costs and other related content, only the overall efficiency of prominent grease is the proper one.
Screen Shot 2013-11-28 at 12.27.53 PM.png
Screen Shot 2013-11-28 at 12.28.27 PM.png
5 ATTENTION OF STORAGE AND USE
5.1 Packing should be sealed to prevent the intrusion of moisture and dust, and should prevent grease oxidation deterioration.
5.2 Try to gentle with grease when transportation and handling processes, it is best to erect, and avoid heavily fell touch, don’t roll the edge of the drum.
5.3 Grease should be kept indoors as much as possible, avoid the sun and rain, if indoor storage conditions not used, take measures to prevent wind and rain.
5.4 Grease should be smooth after use to prevent the oil seperation; can not mix different types of grease, and can not use after heating to melt.
Basics Knowledge of Grease
Web Help Desk
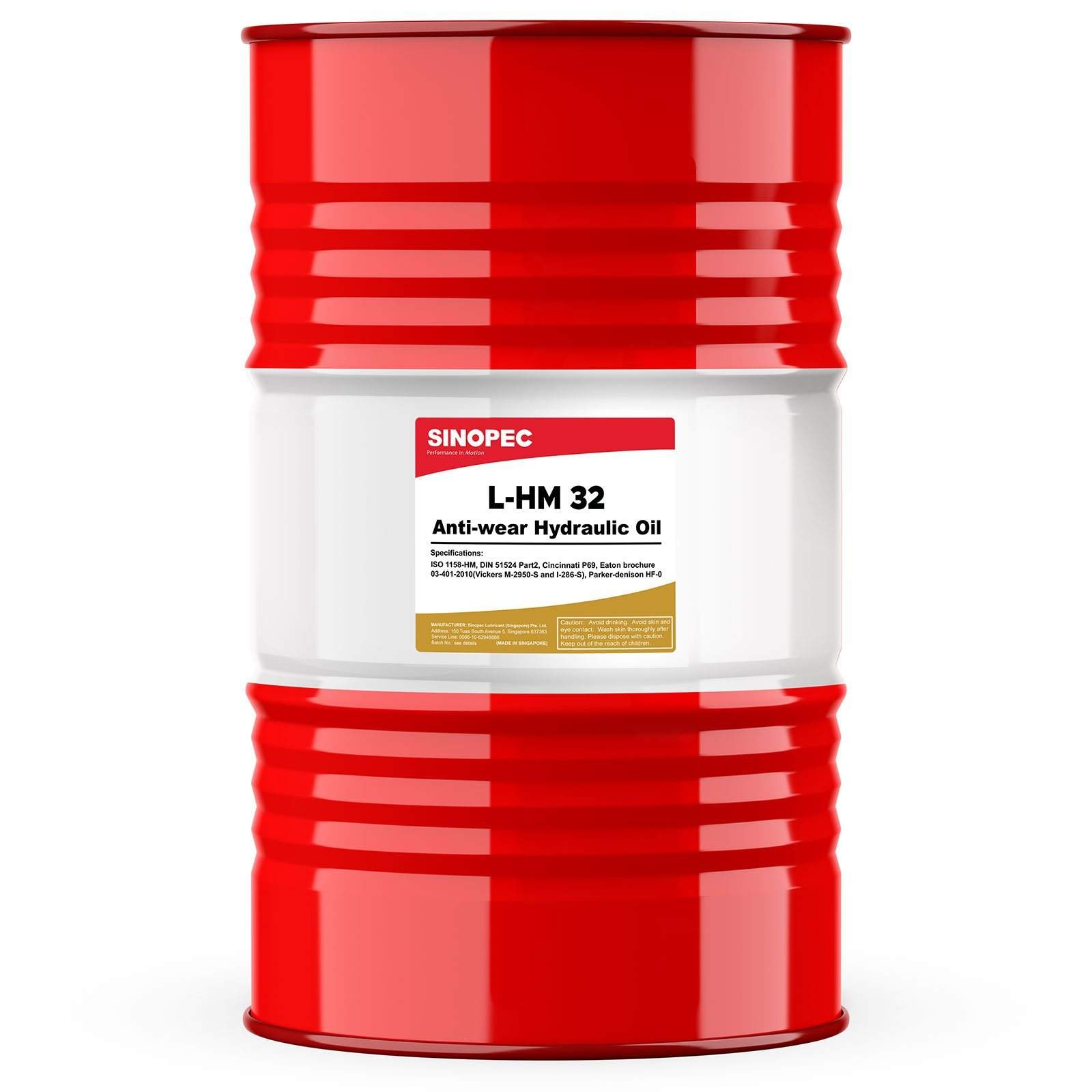
AW 32 Hydraulic Oil - 55 Gallon Drum
Sale price$449.00
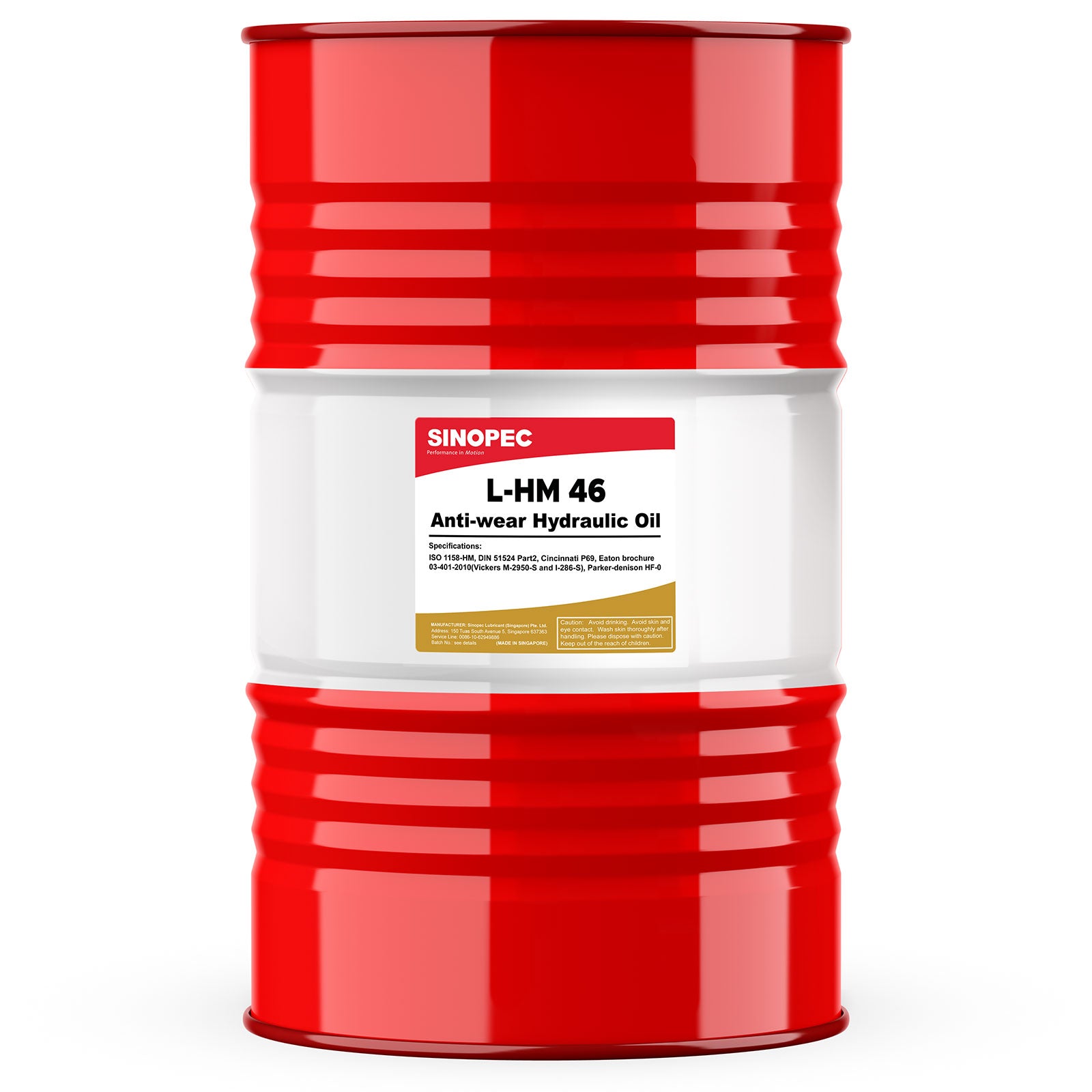
AW 46 Hydraulic Oil - 55 Gallon Drum
Sale price$449.00
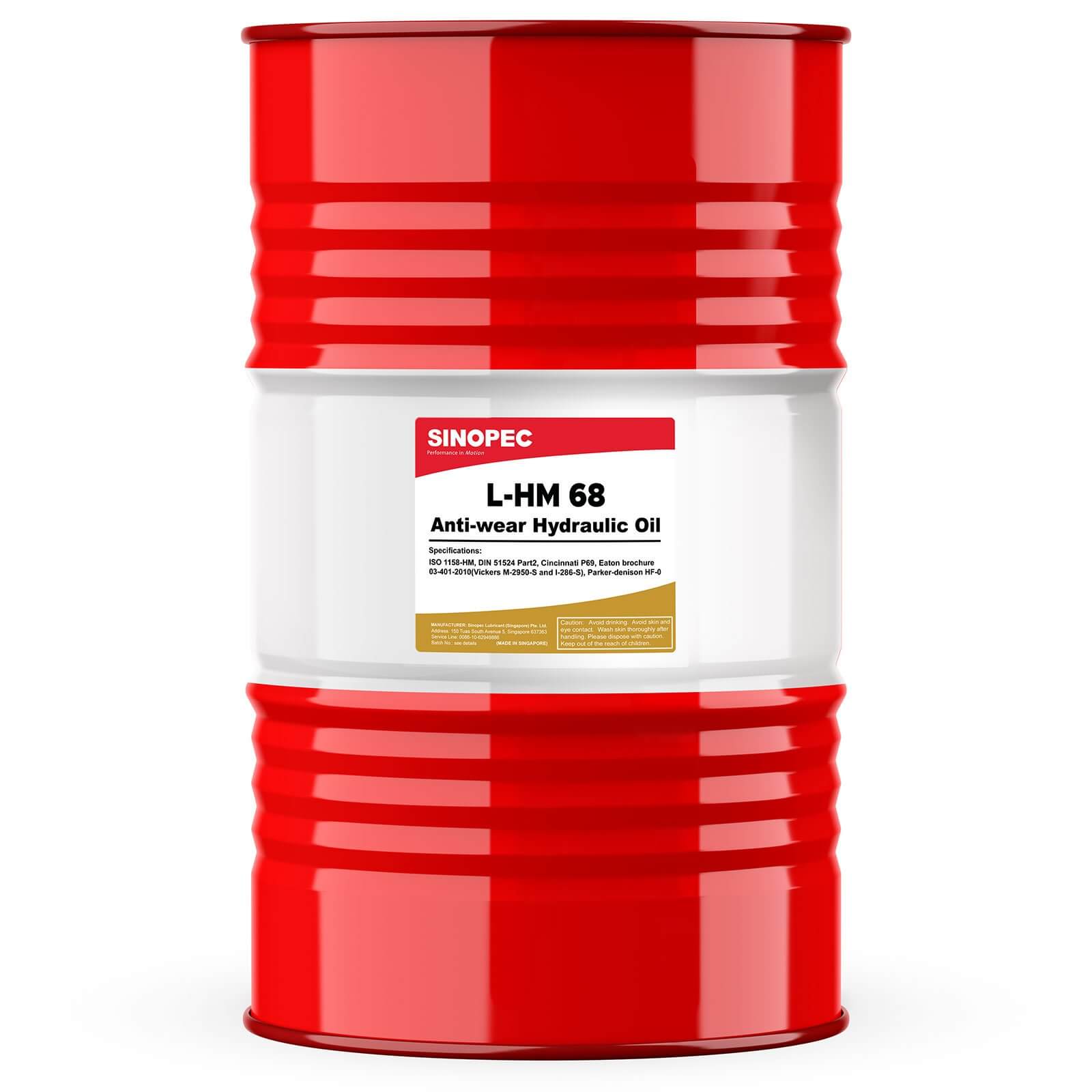
AW 68 Hydraulic Oil - 55 Gallon Drum
Sale price$449.00
Where Do We Ship From